The onus to carry out food safety procedures falls on processors
The federal government may be on shutdown, but federally regulated food safety initiatives remain critically important for food and beverage processors. During the shutdown, now entering its second week, U.S. Department of Agriculture (USDA) meat inspectors will continue their monitoring duties in meat, poultry and egg processing facilities. However, inspectors from the U.S. Food and Drug Administration (FDA), which oversees roughly 80 percent of the American food supply, have been deemed “nonessential” and sent home on furlough. Similarly, the U.S. Centers for Disease Control (CDC), which investigates foodborne illness outbreaks, has placed its epidemiological staff on furlough.
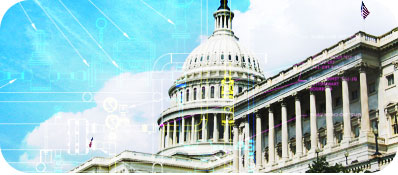
What does this mean for food and beverage processors? First, the responsibility of processors to produce safe, high-quality products does not go away due to a lack of government oversight. If anything, that responsibility has increased. Without government investigatory backup to trace the cause of outbreaks, processors have a greater obligation to ensure that they are only introducing absolutely impeccable products. Business ethics aside, the liability for causing a foodborne outbreak does not decrease in the absence of the FDA and CDC. So vigilance is job one for food and processors, especially now.
Second, this situation presents an opportunity for food and beverage processors to proactively address safety concerns as a public service. Because of the constantly changing regulatory landscape, it is nearly impossible to build a system that will adhere to all future requirements. Therefore, forward-thinking processors are best served by building flexible systems that meet current requirements while leaving room for updates as new safety initiatives evolve. That allows these processors to stay ahead of the game, regardless of what’s going on in Washington. This has a definable benefit for brands; as a consumer, wouldn’t you favor the company that assumed the responsibility for keeping its customers healthy by proactively implementing stricter safety practices?
Wright Process Systems specializes in food safety issues at a plant design and system implementation level. Our process engineering department focuses on the design of sanitary systems such as clean-in-place systems, sterile systems, and other process systems designed specifically to improve food and beverage product integrity. Additionally, our onsite services teams bring industry-leading experience to a range of safety-related work, including:
- Field audits to identify risk contributors
- Equipment overhauls to meet current requirements
- Material or component changes to higher grade sanitary versions
- Reworking piping systems to eliminate historically common non-ideal practices
- Automation and instrumentation upgrades for quality assurance tracking and self-checking
- Operating retraining and coaching for best practices
- Managerial documentation improvements for critical control points