The design-build delivery method offers significant advantages to food and beverage manufacturers. Design-build fulfills the needs of widely differing projects and projects are delivered faster and more cost-efficiently with clear standards for quality control.
This article covers key advice on how to organize projects and identify gaps that exist in traditional approaches that are best addressed by the design-build project format with a food process engineering and construction company.
The Design-Build Project Format
In the design-build approach, the owner manages one contract for design and construction, with a single point of responsibility. The designer and contractor work together as a unified team to provide project recommendations that align with the owner’s schedule and budget.
Any changes throughout the project are addressed by the entire team as a whole for collaborative problem-solving and innovation. While single-source contracting is the major difference between design-build and traditional project delivery, this highly collaborative culture is distinct to the design-build project format.1
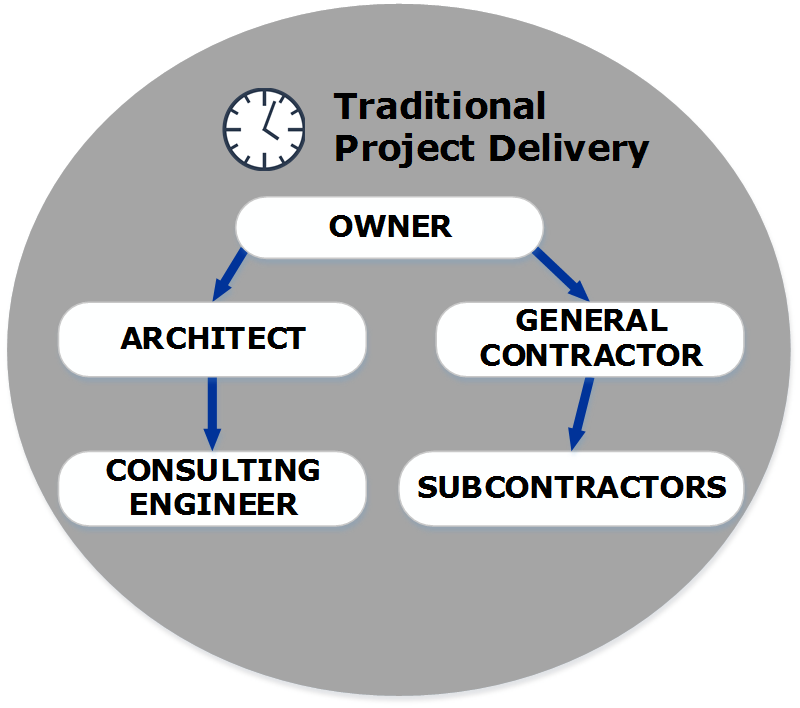
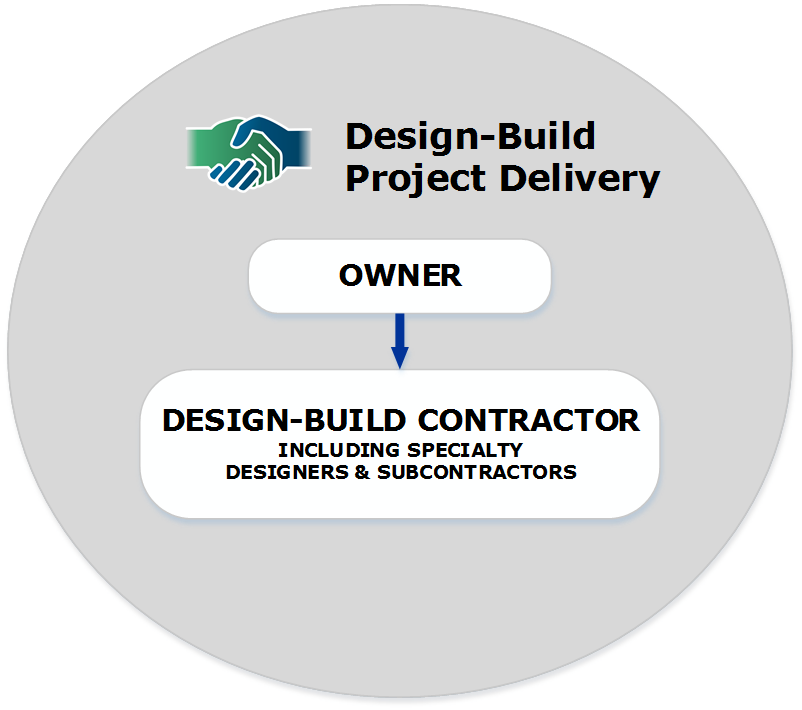
Design-Build and the Food Process Industry
The key piece to design-build in the food process industry is selecting the design-build entity based on their intimate experience and expertise in process design and operations, such that all decisions made throughout the project keep the needs of the end food or beverage product front and center in mind.
In traditional approaches, the architecture and general construction portions of the project stand alone from the process portion. The customer secures an AEC (Architect, Engineer, and Contractor) team to work on the building and site, and separately secures a Process Integrator to install the process system, with little overlap between the two groups.
The separation between the two groups is not intentional: traditional AEC groups are not often well-versed in the operational food-production requirements of the project and unaware of gaps in the designs that will only be discovered in the future as the plant is put to use.
Even the most accomplished AEC building teams, who may have experience in repeating requirements from previous projects, usually do not have first-hand process design engineering expertise integral to the decision-making workflow.
Additionally, AEC teams usually consider process as a general trade and do not engage a process expert until late in the game when bid packages are sent out, well after the project design has been completed.
When the above type of project organization occurs, the process contractor may receive a call to solicit a bid to an AEC team on a new project. At that point, the process contractor reviews the plan and finds areas that can be improved or adjusted to better represent the food process operational aspects of the project, but by then it is too late to make changes and the customer ultimately must accept shortcomings or the added costs of delays and changes.
These shortcomings are preventable by engaging a food process design-build entity from the beginning of the project. When a design-build entity is engaged with knowledge specific to the project type, and when compared to other project formats, the benefits of the design-build delivery method are clear.
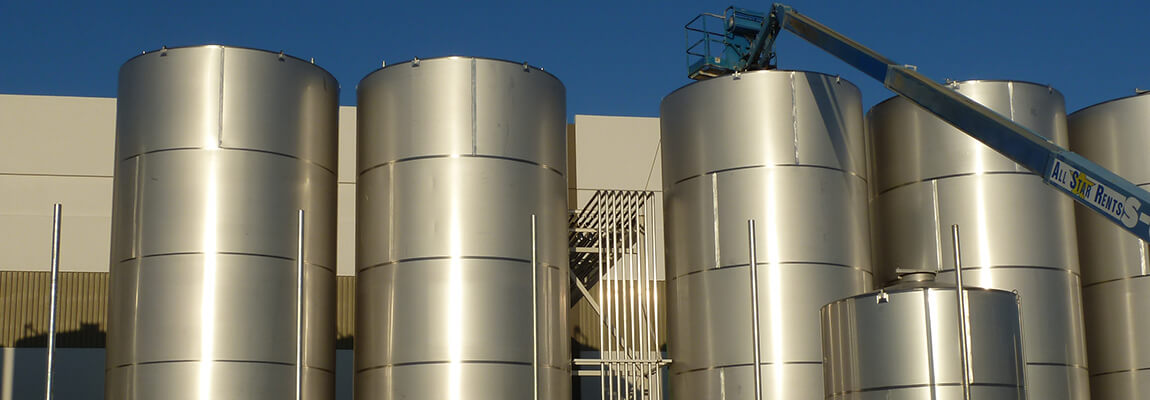
Design-Build Advantages
Selecting a food process contractor as the design-build entity, or as a food process engineering consultant during the development period upstream of securing AEC consultants, brings numerous benefits to the project. Outlined below are the staple offerings that a food process contractor brings to a project:
- Food safety and quality - The food process contractor knows food quality and food safety, and is in the best position to guide design and installation work, ensuring that the client’s sanitary and hygienic requirements are fully met.
- Best practice principles - The food process contractor knows Department of Health, FDA, and USDA regulatory inspection and compliance requirements, and integrates these factors into the design and submittal process from the beginning, which means no lengthy third-party review is required.
- Expedited permitting - The food process contractor knows the permitting process for manufacturing systems and facilities, and will advise on what elements of the project should be included in the permit submittal, and which items are not required by code to be permitted, saving permit review time, cost, and scrutiny.
- Successful installation - The food process contractor has a track record of successful process-specific installations, and can reference past projects and designs to facilitate design review and acceptance by the customer, the AEC team, and regulatory agencies. Most unique city submittals (notably fire and wastewater departments) require examples of previous permitted installations or approvals by other jurisdictions in order to sign-off, where they have not seen such installation in their jurisdiction themselves.
- Building code - The food process contractor knows building code specific to process projects, and can both advise the AEC team and regulatory inspectors on key elements so as to save them from lengthy research and code reviews for unique conditions.
- Manufacturing expertise - The food process contractor understands food manufacturing operations, and can promote and defend the needs of the plant staff during construction.
- Plant commissioning and startup - The food process contractor knows how to startup and commission the process and utility portions of the project, and is in the best position to prioritize and schedule construction and installation work.
- Sanitation best practices - The food process contractor knows 3A, NSF, and industry-specific sanitary construction means and methods, and can design, monitor, and correct the construction and installation workflows of subcontractors and integrators throughout the project.
- Effective plant management - The food process contractor knows manufacturing financial, operational, and functional plant management requirements, and is in the best position to structure project work specific to the plant’s operating basis. Construction work can be sequenced around existing production runs, taking advantage of built-in downtime in order to avoid lost production time. New facility construction can be scheduled so that new employee training, third-party audits, and trial production runs can occur during final building permitting, allowing occupancy and outbound product to be approved as close together as possible.
The design-build approach for food process projects streamlines project workflow with simplified project management. Please contact Wright Process Systems for more information or to discuss your next Design/Build Process project.
Source:
1. “What is Design-Build?” Design-Build Institute of America, dbia.org/what-is-design-build/.