Water
Purity of process, purity of product
Bottled water represents an enormous segment of the beverage market, though the marketplace for bottled water and water-related products has become increasingly crowded. To rise above the fray, bottled water producers need to guarantee absolute purity and unassailable quality. Wright Process Systems can help your bottled water processing facility live up to those ideals. We are experts in sanitary process system design, with specialized capabilities in hygienic process piping, automation, fabrication, general construction, and process improvement engineering.
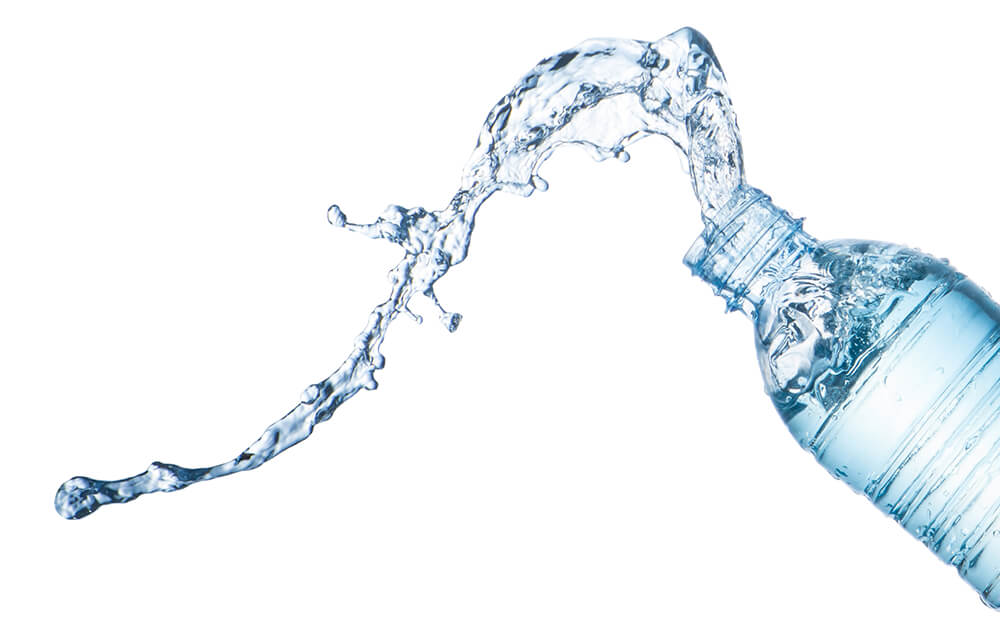
Systems we have designed and installed for the bottled water industry include:
- Automated control systems
- Storage tank systems
- Clean in place (CIP) systems (either skid-based or permanent placement)
- Membrane filtration skids and systems
- Pre-process filtration and straining components
- Water pasteurizers
- Water UV sterilizers
- Ingredient and flavor addition
- Bottling, capping, container handling, and packaging systems
Sport & Energy Drinks
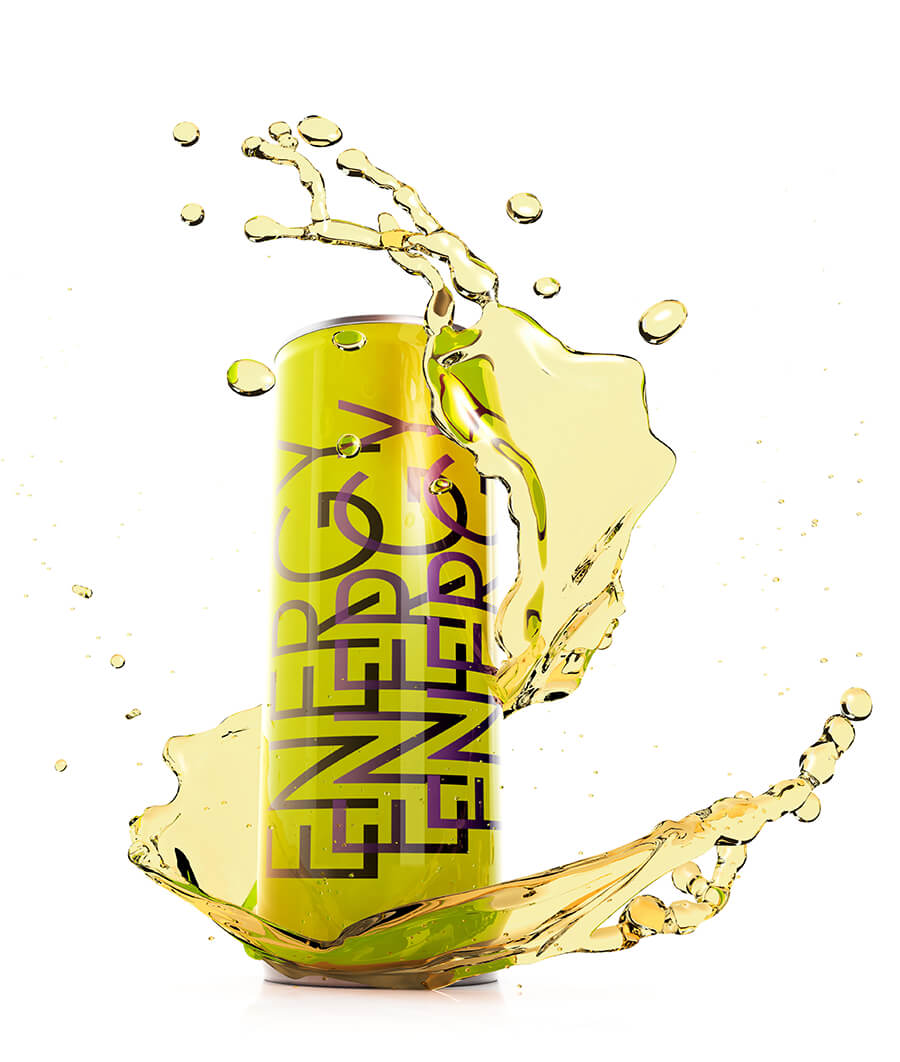
Consistent performance yields premium quality
Blending a variety of ingredients into one, proprietary beverage, sport and energy drinks require absolute consistency across batches to maintain a producer’s brand advantage. For years, Wright Process Systems has worked with sport and energy drink producers to streamline their processes, upgrade their facilities, and provide new solutions to optimize their systems. We combine specialized experience in sport and energy drinks with cross-industry insights gained from work in related fields to create customized solutions for your specific process.
Systems we have designed and installed for the sport and energy drink industry include:
- Ingredient receiving and storage systems
- Liquid sugar and water piping installations
- Blending tanks and routing flow-verter panels
- Bottling line feed piping routing system
- Batch and blend systems
- Powder ingredient liquification, blending, conveyance, and handling systems
- Automated ingredient and concentrate routing piping, including automated routing valves
- Storage tank systems
- Clean in place (CIP) systems (either skid-based or permanent placement)
- Flow transfer panels
- High-speed inline beverage mixing systems
Juice
Maximum yield and product consistency from the industry’s leading beverage process solutions provider
When producing juice, product consistency is critical. Product clarity, microbial stability, and yield are some of the most difficult variables to manage, yet they need to be absolutely uniform from one container to the next. Wright Process Systems understands the juice industry and how to make your system more uniform and more efficient. We also have the design, construction, fabrication, and installation resources to build you a new sanitary juice production facility from the ground up, using solutions such as ultra filtration modular systems that provide ideal product clarity over maximum yield with a minimal footprint.
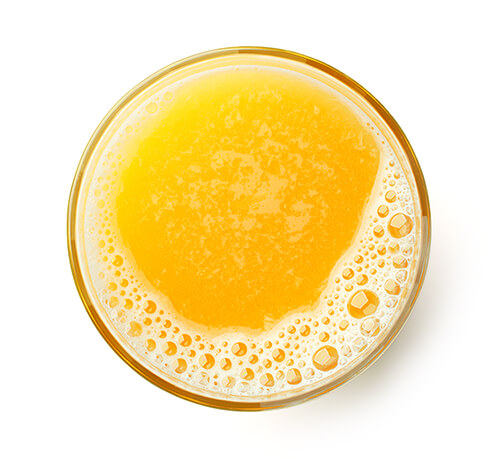
Systems we have designed and installed for the juice industry include:
- Shop-fabricated, state-of-the-art membrane filtration systems
- Complete pressed-juice process rooms
- Bulk fruit receiving, unloading, sorting, and conveyance systems
- Juice concentrate evaporators and condensers
- Juice pasteurizers
- Mixproof valve routing and distribution circuits
- Ingredient receiving and storage systems
- Liquid sugar and water piping installations
- Bottling line installations
- Automated ingredient and concentrate routing piping, including automated routing valves
- Storage tank systems
- Tanker loading, unloading, scaling, and CIP systems
- Clean in place (CIP) systems (either skid-based or permanent placement)
- Flow transfer panels
- High-speed inline beverage mixing systems
Carbonated Beverage
Wright Process Systems has designed, built, and serviced numerous carbonated beverage process systems, adhering to the strictest codes and regulations while engineering forward-thinking solutions that help our carbonated beverage clients stay ahead of the competition.
Systems we have designed and installed for the carbonated beverage industry include:
- Ingredient receiving and storage systems
- Mixproof routing and distribution circuits
- Batch and blend systems
- Bulk sugar and ingredient handling
- Liquification, high-shear blending, and other pre-processes
- Concentrate blending and transfer systems
- Automated control systems
- Storage tank systems
- Clean in place (CIP) systems (either skid-based or permanent placement)
- Flow transfer panels
- Bottling, capping, container handling, and packaging systems
- Drum and tote unloading
- Carbo-coolers and carbonation injectors
- Facility Modifications—floors and floor drains, ceiling alterations, sanitary wall finishing
- Processing equipment installation, including tanks, pumps, valves, and complete process piping
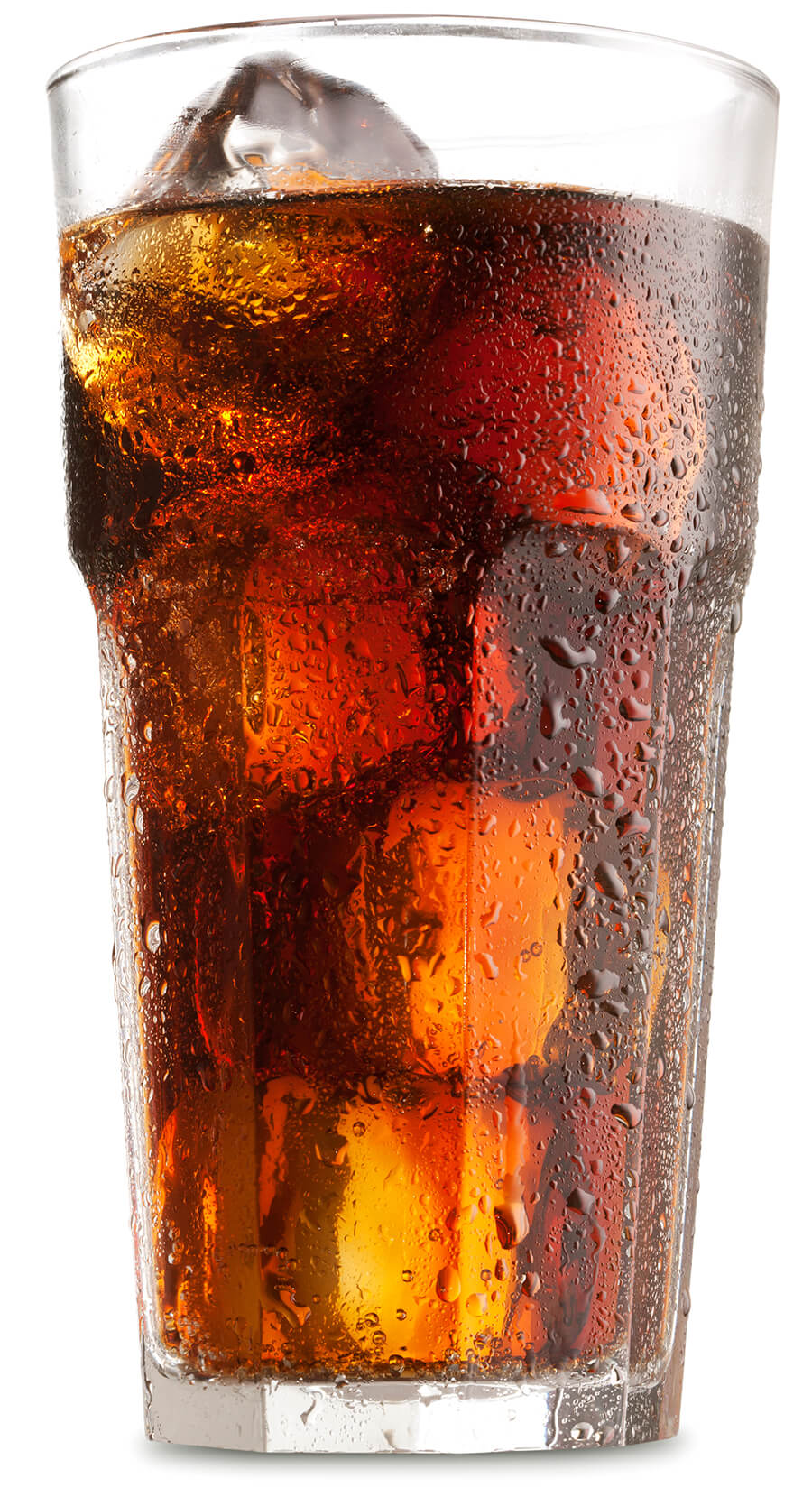