Forward-thinking process design is critical for automation implementation
When building a new process plant, or designing a new system, process engineers must consider an automation system’s necessary features, overall cost, scalability, and ongoing maintenance. Experienced process engineering companies like Wright Process Systems consider variables such as:- What does the system need to do now?
- What will the system need to do in the future?
- What are the costs to purchase, install, maintain, and upgrade the system over time?
- What does it take to maintain and service the system?
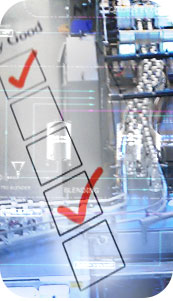
Some plants benefit from more basic automation solutions that their existing in-house staff can maintain and service. Other plants, with more complicated automation needs and a larger scale of production, can justify the greater expense of a state-of-the-art solution that requires regular maintenance from an outside service provider (or the hiring of an in-house expert to handle the maintenance). Determining the correct solution for your plant requires partnership with a company that’s dedicated to continuous process improvement. Contact Wright Process Systems to learn more about how a forward-thinking automation system can benefit your plant.